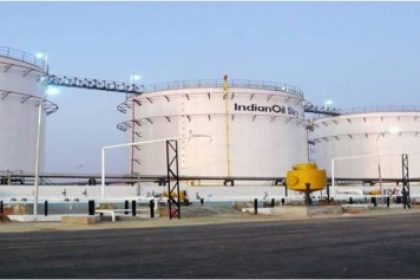
Steam generation is integral in the process industry and plays an indispensable role in performing processing operations. Steam is ideal for passing through tubes and transferring heat uniformly, as it can hold a substantial amount of energy. Fuels are burned in the furnace that boils the water and generates steam and then carried for the processing, where needed. Although steam is essential, condensate is inevitable in any boiler system. Condensate is the energy released by steam as water that needs to be discharged from the boiler system to ensure efficient processing.
What is a Steam Trap?
Steam traps are automatic valves that hold the steam until it releases energy and condenses into water. The water is eliminated, preventing the loss of efficiency in the steam boiler. Neglecting the removal of condensate may cause water hammer that result in damage to valves, equipment, and tubes in the system.
Importance of Steam Trap:
Steam is generated when the water is vaporized and formed as gas. For vaporization to take place, the water molecules must contain sufficient energy to break the bonds between the molecules. The energy in water molecules that converts the liquid into a gas is known as ‘latent heat.’
The boiler system utilizes latent energy in the steam that is transferred to accomplish process operations. Once the steam loses its latent energy it begins to condensate. Failing to discharge condensate quickly affects the heat transfer and may cause corrosion and water hammer, resultantly reducing the efficiency of the boiler.
Types of Steam Trap in Boilers:
Steam trap performs its primary function of separating steam and condensate, but different types of steam traps use varying mechanisms to discern between steam, air, and condensate. Some of the widely used steam traps are as follows:
1. Inverted Bucket Traps:
As the name suggests, inverted bucket traps consist of an inverted bucket that functions on the principle of buoyancy. The bucket rests at the bottom of the steam trap while the valve is open. The steam and the condensate flow under the bottom of the inverted bucket after moving into the trap. The steam accumulates at the top of the bucket, the bucket inclines upwards and closes the discharge valve. Once the steam is condensate, the condensate fills the bucket that falls and opens the discharge valve that passes the condensate.
2. Ball Float Steam Trap:
A ball float steam trap consists of a ball float connected to a trap discharge valve submerged underwater to avoid steam loss. The condensate enters and accumulates in the float chamber, causing the float to surge upwards. It results in the opening of the discharge valves to pass the condensate. An in-built thermostatic air-vent assists in releasing air to facilitate quick functioning.
Ball float steam traps are extensively used for heating operations during processing because of the continuous discharge of condensate immediately after its formation, high thermal efficiency during both light and heavy loads, and high resistance to water hammer.
3. Thermostatic Steam Traps:
The difference between the temperatures of steam and condensate contributes to the working of thermostatic steam traps. Steam has more temperature than condensate, indicating the port in the thermostatic steam trap to shut when the temperature exceeds its predetermined range and open when it is reduced. The port allows the passing of condensate along with cooler air and CO2.
4. Thermodynamic Steam Traps:
The working of thermodynamic steam traps is based on the thermodynamic principle and depends on the flash steam formed from condensate. Factors such as compact size, single moving part, wide pressure range, and corrosion resistance are the reasons for its wide range of applications.
Factors to Consider while Selecting Steam Trap:
- Air Vent:
During the beginning or ‘start-up’ of a process operation in a boiler system, the heating space is filled with air which, if not replaced, can reduce the heat transfer and accelerate the time required for warm-up, leading to low efficiency. Hence, it is essential to remove air as soon as possible before it blends with the steam. The only way to separate air and steam is through condensing steam. Although it can be accomplished with a steam trap, an air vent is required in large systems. Float traps with in-built air vents are ideal in such situations.
- Discharging of Condensate:
It is necessary to ensure that the trap passes the condensate and captures the steam as the steam leakage would cause a high loss of efficiency. Condensate needs to be released immediately for optimal heat transfer.
- Process Requirements:
Before choosing a steam trap, it is essential to know the operations to be performed in the process plants by considering the factors such as maximum pressure for steam and condensate, operating pressure for steam and condensate, temperature, and flow rate.
- Reliability:
A reliable steam trap of excellent quality ensures that the steam is trapped and distributed for processing effectively. Lack of reliability in the steam trap may cause accumulation of dirt, corrosion, and water hammer.
Rakhoh Boilers is one of the leading boiler companies in India with 38+ years of expertise in manufacturing efficient steam boilers for process industries worldwide. We provide the best boiler services like steam trap assessment, energy audit, boiler automation, annual maintenance contract, etc., to upgrade boiler performance and lifecycle.