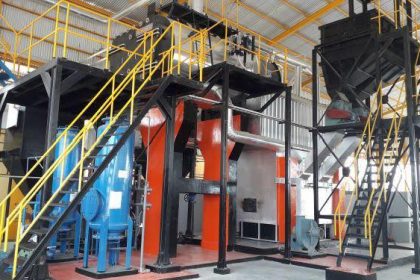
Since boilers are a crucial part of the processing industry, manufacturers strive to supply the industry with boilers that are efficient, cost-effective, and long-lasting. The rubber industry requires highly efficient and sturdy boilers to ensure the smooth processing of raw rubber into the final product used extensively for many purposes.
Rubber is utilized in many industries and fields, serving different purposes. The most important among them are rubber tyres in vehicles that are responsible for the balance and carrying the weight of the concerned vehicle. Therefore, the rubber for tyres must be of supreme and sturdy quality. Apart from tyres, it is used for machinery, medical, construction, mining, electronic devices, and household equipment.
Rubber is mainly of two forms namely, Natural Rubber and Synthetic Rubber. With the processing operations, it is manufactured into rubber products.
Difference between Natural Rubber and Synthetic Rubber:
Natural Rubber is latex that is a sap-type milky material found in more than 2,500 plants. Latex for commercial use is found in a tropical tree named ‘Hevea brasiliensis’ and contains polyisoprene polymer. Whereas rubber is a specific form of polymer that can flex and stretch called ‘elastomer’
However, over 70% of the rubber used nowadays is synthetic rubber. Synthetic rubber is developed through the process of polymerization, wherein the molecules are linked together in long chains. The development of synthetic rubber has continued and advanced through the years.
Manufacturing of Rubber with Steam Boilers:
Rubber arrives in processing plants in either natural or synthetic form and undergoes four processes to complete its manufacturing. These four processes are Compounding, Mixing, Shaping, and Vulcanizing. It is noteworthy that the compounding process depends on the intended product of the rubber.
Compounding:
Compounding is the process wherein, chemicals and additives are included to modify the rubber, depending on the final product. The chemicals added during the compounding process react with the rubber later in the vulcanization process to stabilize its polymers. Other additives used during the compounding process are Reinforcing fillers, Non-Reinforcing fillers, Color pigments, antioxidants, ozone-resistant chemicals, softening oils, and others.
Carbon black acquired from soot is one of the majorly used reinforcing fillers. It increases the strength and improves the resistance to tearing and ultraviolet depreciation of rubber. Therefore, most of the rubber products are in black.
Mixing:
It is important that the mixing of the additives is accomplished accurately in a rubber, which is difficult considering the high viscosity found in rubbers. Because of this, an increase in temperature is required. But, raising the temperature of rubber to 200 degrees Fahrenheit may cause premature vulcanization. To avoid such situations, mixing is achieved in two stages, in which carbon black is added first to the rubber and then followed by other chemicals and additives once the rubber gets cooled in the second stage.
Shaping:
Shaping of the rubber can occur in 4 different ways– calendering, casting, coating, and extrusion. The calendering process takes place by passing the rubber through a set of rolls to acquire the desired thickness. Casting occurs by dipping or casting a negative mold in a rubber bath and later dried with cross-linking. The coating is applying a coat of rubber to other materials such as tents, raincoats, etc. The extrusion process occurs by forcing plastic rubber through numerous screw extruders.
Vulcanization:
Vulcanization (also known as curing) is the final process that completes the manufacturing of rubber. Cross-linking in rubber begins from the mixing process but at an initial level. Vulcanization takes place after the process of shaping; which heats the rubber through hot steam of about 200 degrees Celsius that resultantly increases the vulcanization rate. In steam vulcanization, the processing operation takes place by direct contact of steam with the rubber. It is, therefore, essential to conduct regular treatment of the steam as the direct contact leads to its impurity. Because steam has a high vulcanization capacity, boilers must be maintained properly as per the guidance of the steam boiler manufacturer to ensure smooth running.
Rakhoh is one of the leading names in steam boiler manufacturers. We have manufactured and installed highly efficient and sturdy boilers for many manufacturing industries by understanding their respective demands and requirements.
In the case of rubber manufacturing industries, it is prudent to ensure that the steam boiler used is:
Adaptable to the Fluctuating Demand: The steam demand in a rubber processing plant may increase or decrease various times, depending on the product. Fluctuation is one of the most faced difficulties in a rubber processing plant.
Efficient in Energy: One of the trials faced by rubber processing plants is to reduce the fuel consumption and energy output of the boiler. A boiler that generates higher steam output and demands minimum energy is ideal for rubber manufacturing.
Reduced Emission: Steam boilers that reduce greenhouse emissions and comply with sustainability are suitable for any processing units to preserve nature.
Learn more about Rakhoh’s Boilers and Services on http://www.rakhoh.com
FAQ:
1. Which kinds of Boilers are suitable in the Rubber Industry?
Nowadays, Water Tube Boilers are preferred over Fire Tube Boilers as they help in saving fuel and resources and ensuring longer life of boilers
2. How to know that the selected steam boiler would reduce greenhouse emissions?
Ask your steam boiler manufacturer for a product rated for low CO2 emissions.